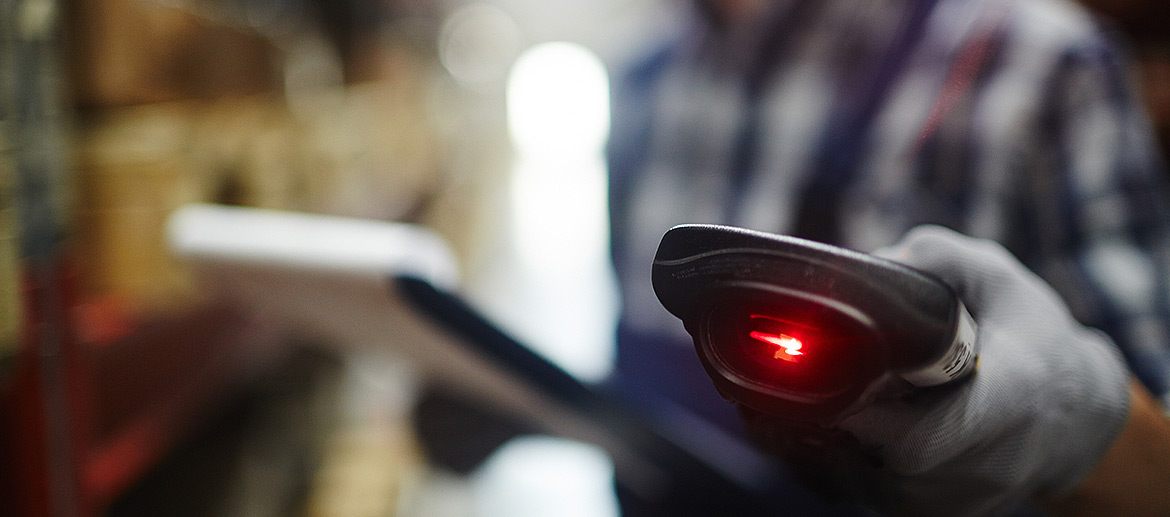
Vendor-Managed Inventory
VMI is an inventory management approach in which a supplier or vendor (the inventory seller) manages and maintains the inventory, even after the inventory is in the customers (the inventory buyer’s) warehouse. The supplier takes all inventory-related decisions and replenishes inventory levels for the customer.
With this approach, the vendor is responsible for minimizing the customers inventory stockout and overstocking risks. They do this by using inventory management software that allows them to set stock thresholds, monitor inventory levels, and maintain these levels at a targeted level.
When should VMI be used?
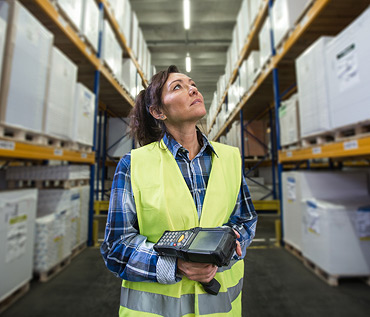
The VMI approach is best used by companies that use many types of products from many different vendors. When multiple vendors are involved, companies may find it burdensome to manage the incoming inventory from all of them. Shifting the responsibility for inventory management to various vendors reduces the burden. It also enables the vendors to proactively and quickly replenish the customers stock, making sure they always have the parts they need to get the job done. Given DFP resells a multiple of difficult product lines, we are well-suited to offer VMI services. Contact Us to learn more.
Benefits
DFP customers realize VMI system benefits by achieving better inventory accuracy, forecasting, and service. With this approach, DFP can also reduce inventory-related costs (for both parties) as we employ necessary tools and software to manage inventory, replenish stock and reduce costly overstocking.